Snag a piece of 1/2X6x36 aluminum. D/T holes wherever. The difficulty in explaining is that you will have to control at least two axis in the fixturing.
Imagine a bolt down through an action hole... that's an easy place for the rear "pivot". Set Z axis with whatever convenient.
You'll have 2 options on this fixture plate when running across a spindle moulder* . You can use a rub collar on the spindle,is how curves are normally done.... or use a fence to index off of. Your question is tough because,well money. That piece of aluminum plate will come in handy for a variety of uses.... when you get a mill.
Showing up at a cabinet shop,or job shop with stock in hand....well,bust out your wallet. Show up with your stock on a plate? Take about 15 minutes.... and they certainly don't want the fixture.
*Spindle moulder... shaper,router,or mill. Any piece of equipment with a spindle,usually referenced as a vertical. Think vert vs horizontal mill... in the woodshop they're almost always verts.
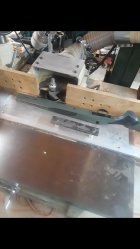
Imagine a bolt down through an action hole... that's an easy place for the rear "pivot". Set Z axis with whatever convenient.
You'll have 2 options on this fixture plate when running across a spindle moulder* . You can use a rub collar on the spindle,is how curves are normally done.... or use a fence to index off of. Your question is tough because,well money. That piece of aluminum plate will come in handy for a variety of uses.... when you get a mill.
Showing up at a cabinet shop,or job shop with stock in hand....well,bust out your wallet. Show up with your stock on a plate? Take about 15 minutes.... and they certainly don't want the fixture.
*Spindle moulder... shaper,router,or mill. Any piece of equipment with a spindle,usually referenced as a vertical. Think vert vs horizontal mill... in the woodshop they're almost always verts.
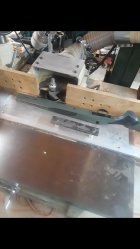