My hardware is a week out, so I'll explain using another stock in the pics.
Mark your centerline from your stock onto your cheek piece.
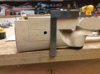
When you have your hardware in hand, put the lock screw in the base and lightly screw it together. Measure the length of the screw and nut, add whatever extra dimension you added on the stock side and drill your side hole that deep. Lay your stock on it's side and drop the nut in the hole. Orient the squared sides of the nut properly and slide the base into the pocket. If it won't go, drill the hole a tad deeper until the base slides in, then install the screw till it's lightly tight. Your base should now swivel slightly on the screw. Adjust the screws in your top hardware piece to where you want it. It can be adjusted for movement, side to side. I leave about 2/3 of my movement on the left side. Drop your top piece into the lower. Measure your distance from the side of your blank and use that to lay out your cheek piece cut.
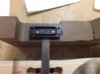
Then, clamp your cheek piece in your jig. Set up your straight edges and stops for the route. Use a 1/4 straight cutter for this cut. Add a 1/16 to the length of the cut on each end. Just one tip: Make a shallow cut first and check your fit. Adjust your straight edges to get a snug fit for the width. You want to be able to push the hardware in the slot, forward and back into the extra length, but just barely. It should fit snugly enough so that it won't move when held upside down. This AIDS in the install. When it's right, finish the cut to proper depth. Put the hardware 1/16 below the surface.
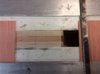
Pull the piece from your jig, press your hardware into the cut and drop it into the base in your stock.
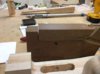
If you have a gap, push the cheek piece back towards the rear. Because you have a tight fit, the hardware will hold the position when you gently pull it out to install the screws. If you don't have a tight fit, you can apply painter's tape to the side of the hardware to get it. You can also try to make the top hardware inlet "dead nuts on". Good luck with that. Maybe you'll hit it right. My method shaves an hour off going back in the jig for "recuts", trying to get rid of that 1/16 gap.