Hi, working on a induction annealer. Using one of the many 1000 watt zvs amazon boards and a 48 volt 600 watt power supply. Working good enough so far (i think) but wanted to get some input on my results. Below are the images of a case with tempilaq. This is with the shoulder and top of the case in the coil, 6 second anneal time. Red = 1000 f, green = 750 f, grey = 450 f. I get similar results at 4 or 4.5 seconds with the case in the center of the coil. When annealing in a dark room, I've timed it out so annealing stops right before the top of the case begins to glow or maybe just the most subtle of glow.
Anyone with experience with annealing have any input? Should the 750 paint be showing more signs of change farther down the shoulder, etc.? Appreciate any opinions/advice. Edit: Working with 308 lapua brass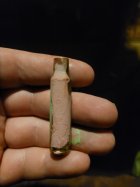
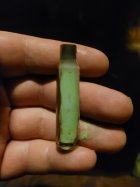
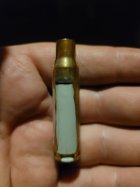
Anyone with experience with annealing have any input? Should the 750 paint be showing more signs of change farther down the shoulder, etc.? Appreciate any opinions/advice. Edit: Working with 308 lapua brass
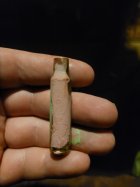
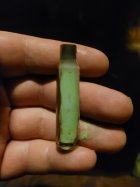
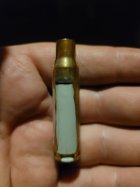
Last edited: