I have never reloaded in my life. After buying an F-T/R .308 I had to take the plunge. I've purchased quite a bit of equipment that needs a home so a reloading bench is next on my project list. Figured I'd document the build. Hopefully some useful information will be shared. It's really more than just reloading bench. I'm planning on doing general gun work on it as well. I'm overtaking a spare bedroom to house the bench, safes etc... More on that later.
I've saved about a bazillion pics of reloading benches and benches in general and I've based my design on those along with input from regular woodworking benches and such. I have a pretty nice woodworking shop at my house so milling lumber etc.. is no issue. The bench will be built from regular construction lumber that I bought a Lowes along with 3/4" plywood, mdf and melamine.
No formal drawings. I'm working from my usual hand scrawled diagrams. Bench top has a finished size of 80x30. The work surface will be 3/4" almond colored melamine with 2 layers of 3/4" mdf glued and screwed together underneath it. The 3rd layer is just around the edge to support the edge banding. Completed top will be edge banded with 1 1/4" x 2 1/2" pine. The base is 68" x 22" and 35" tall made from more construction lumber milled to 1 1/4" thickness.

I've used lots of construction lumber for such projects before and I've learned to buy oversize and mill to finish widths. Here are the leg parts milled and cut to rough dimensions. These will be finished to 3 3/4" x 3 3/4".

And the glue ups.

Next was the milling and cutting to rough dimensions of the base parts.

I've also learned that these pieces are likey to warp and/or twist so I stack and weight them until I'm ready to continue.
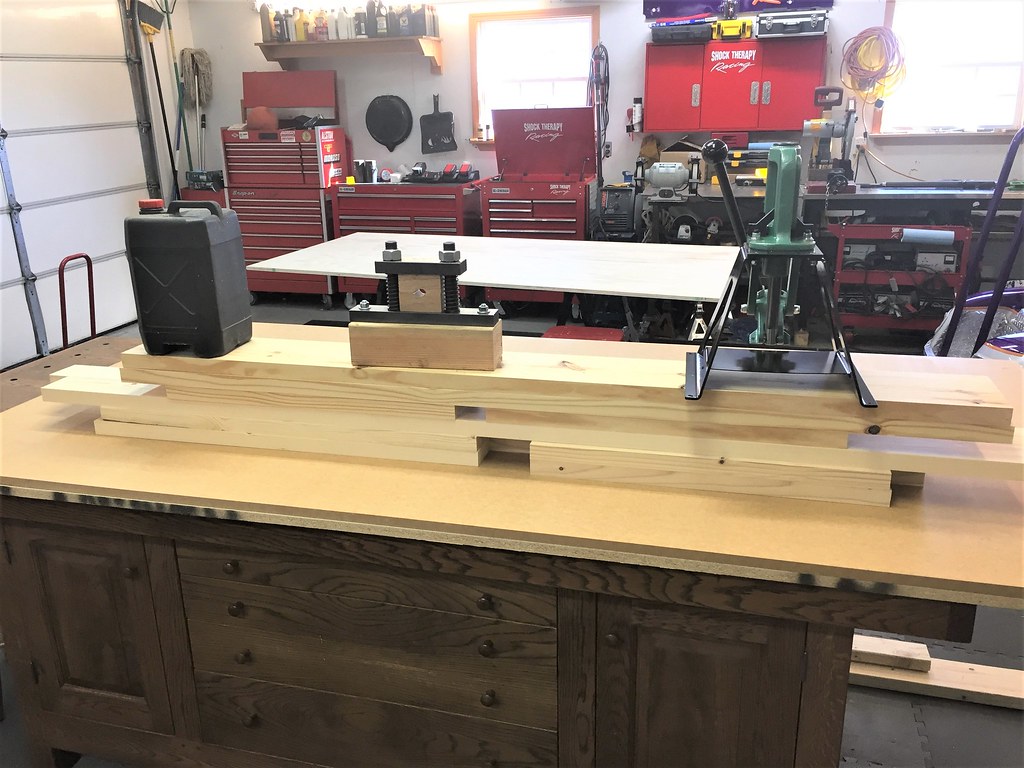
Next is cutting the sheet goods for the top. I'm very blessed to have a nice table saw with Exactor sliding table for such. I also have my shop arranged so that full sheets are supported by benches on both sides of the table saw. Makes working with full sheets by myself a breeze.




Also in the lessons learned category is the way I make the sandwich of sheet goods for the top. I cut the center layer of mdf to perfect dimensions and then use my router with a flush trim bit to size the top layer that I've cut 1/4" oversize. Very difficult to screw the layers together perfectly if they are all cut to exact size and the flush trim bit produces a perfect edge on the melamine.

Hope someone enjoys the pics and the process. I'll post more as I go.
I've saved about a bazillion pics of reloading benches and benches in general and I've based my design on those along with input from regular woodworking benches and such. I have a pretty nice woodworking shop at my house so milling lumber etc.. is no issue. The bench will be built from regular construction lumber that I bought a Lowes along with 3/4" plywood, mdf and melamine.
No formal drawings. I'm working from my usual hand scrawled diagrams. Bench top has a finished size of 80x30. The work surface will be 3/4" almond colored melamine with 2 layers of 3/4" mdf glued and screwed together underneath it. The 3rd layer is just around the edge to support the edge banding. Completed top will be edge banded with 1 1/4" x 2 1/2" pine. The base is 68" x 22" and 35" tall made from more construction lumber milled to 1 1/4" thickness.

I've used lots of construction lumber for such projects before and I've learned to buy oversize and mill to finish widths. Here are the leg parts milled and cut to rough dimensions. These will be finished to 3 3/4" x 3 3/4".

And the glue ups.

Next was the milling and cutting to rough dimensions of the base parts.

I've also learned that these pieces are likey to warp and/or twist so I stack and weight them until I'm ready to continue.
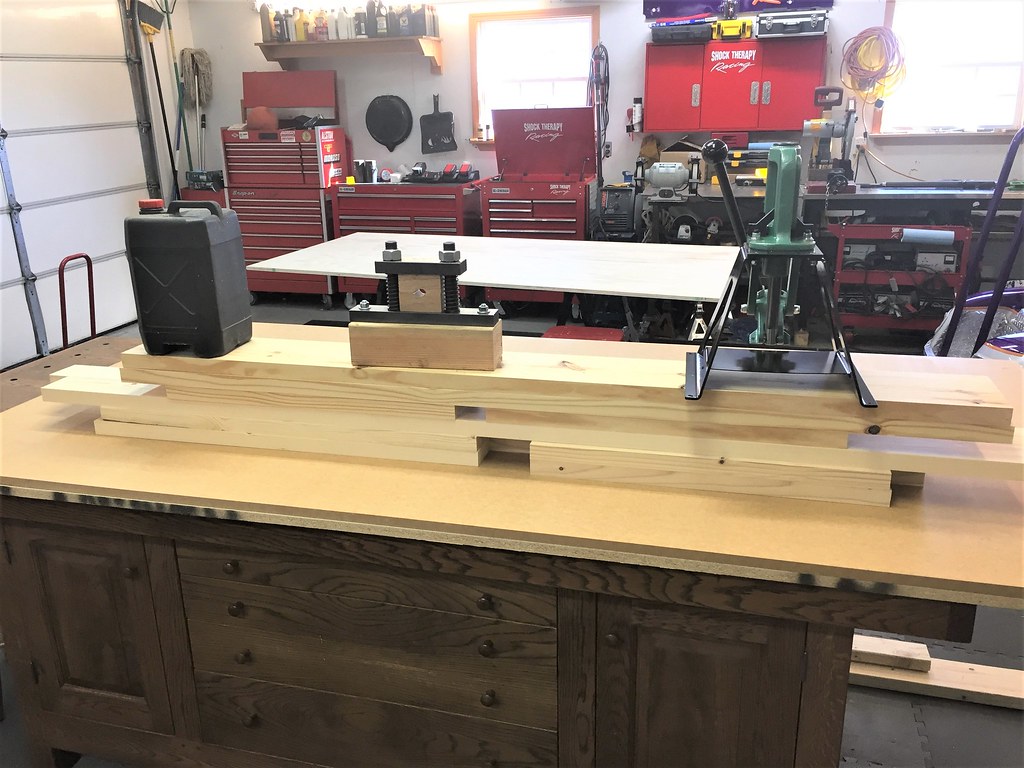
Next is cutting the sheet goods for the top. I'm very blessed to have a nice table saw with Exactor sliding table for such. I also have my shop arranged so that full sheets are supported by benches on both sides of the table saw. Makes working with full sheets by myself a breeze.




Also in the lessons learned category is the way I make the sandwich of sheet goods for the top. I cut the center layer of mdf to perfect dimensions and then use my router with a flush trim bit to size the top layer that I've cut 1/4" oversize. Very difficult to screw the layers together perfectly if they are all cut to exact size and the flush trim bit produces a perfect edge on the melamine.

Hope someone enjoys the pics and the process. I'll post more as I go.
Last edited: