A little insight into what I am doing and why.
I've had a DRO PRO digital readout for my lathe on the shelf for a while and finally decided to get it installed. X axis scale and reader went on the cross slide like a piece of cake. Z axis scale and reader were a whole 'nother story. My lathe is set with it's back to a wall in my garage. This portion of the install was about to cripple me as bending over the bed to mount and level the scale on the back of the bed as well as fabbing the reader mount on the back side of the apron was just adding agony to the situation so out comes the sections of black pipe and I roll the lathe out into the middle of my single car garage so I can actually work on the back from the back. I finish mounting the scale and reader and now it's time to put the lathe back where it was. After rolling it back into place I start to level the bed after which I will tweak it so the center axis of the spindle is parallel to and level to the bed ways.
Back to the leveling of the lathe, this is where my sanity comes into question.
I'm using an Starrett 8" machinist level which I bought new many years ago, it has never been dropped or abused in any way. I decide to check it so I place it on my Kurt vice which is on my Bridgeport. Picture 1 shows where the bubble is after about a minute. Flipping the level end for end, picture 2, shows the identical position of the bubble and the fact that the level is adjusted correctly. Yeah, I know my Bridgeport isn't level with the world.
Moving the level to the ways of the bed, picture 3, shows the bed is very close to level on the X axis.. Flipping the level end for end in the exact same location on the bed ways is where the wheels come off so to speak. Keep in mind that the bottom of the level as well as the ways are squeaky clean and location is exactly the same.
Thoughts?
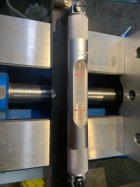
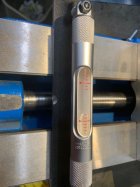
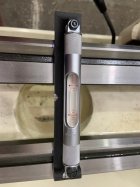
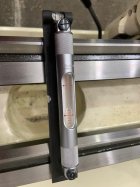
A suggestion from forum member ljmontano was to put 1-2-3 blocks on the way flats and check the X axis level. As can be seen, the bubble offset is the same when the level is flipped end for end.
THANKS LARRY!!!
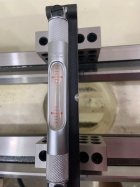
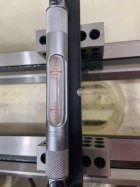
I am still confused in regards to the difference in bubble location when the level is placed on the inverted V ways of the bed.
Anybody have an explanation?
I've had a DRO PRO digital readout for my lathe on the shelf for a while and finally decided to get it installed. X axis scale and reader went on the cross slide like a piece of cake. Z axis scale and reader were a whole 'nother story. My lathe is set with it's back to a wall in my garage. This portion of the install was about to cripple me as bending over the bed to mount and level the scale on the back of the bed as well as fabbing the reader mount on the back side of the apron was just adding agony to the situation so out comes the sections of black pipe and I roll the lathe out into the middle of my single car garage so I can actually work on the back from the back. I finish mounting the scale and reader and now it's time to put the lathe back where it was. After rolling it back into place I start to level the bed after which I will tweak it so the center axis of the spindle is parallel to and level to the bed ways.
Back to the leveling of the lathe, this is where my sanity comes into question.
I'm using an Starrett 8" machinist level which I bought new many years ago, it has never been dropped or abused in any way. I decide to check it so I place it on my Kurt vice which is on my Bridgeport. Picture 1 shows where the bubble is after about a minute. Flipping the level end for end, picture 2, shows the identical position of the bubble and the fact that the level is adjusted correctly. Yeah, I know my Bridgeport isn't level with the world.
Moving the level to the ways of the bed, picture 3, shows the bed is very close to level on the X axis.. Flipping the level end for end in the exact same location on the bed ways is where the wheels come off so to speak. Keep in mind that the bottom of the level as well as the ways are squeaky clean and location is exactly the same.
Thoughts?
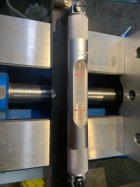
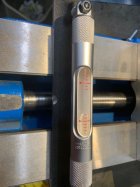
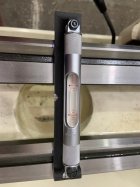
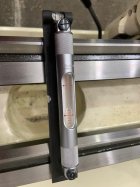
A suggestion from forum member ljmontano was to put 1-2-3 blocks on the way flats and check the X axis level. As can be seen, the bubble offset is the same when the level is flipped end for end.
THANKS LARRY!!!
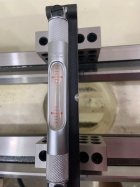
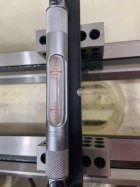
I am still confused in regards to the difference in bubble location when the level is placed on the inverted V ways of the bed.
Anybody have an explanation?
Last edited: