I recently picked up a new to me G0750G with aftermarket DRO for a steal that is less than 2 years old. I'd been waiting to try and find a 13x40 Clausing for over a year but then this came up 15 minutes down the road from me - 2 hours later it was in my shop.
After a good cleaning and alignment it appears the bed has a slight spring in it that I still need to get sorted out for working down the bed, but through the headstock all indicates as well as I might have hoped.
I've come across two things that seems like obvious design flaws for a "gunsmithing" targetted lathe though. Well maybe not design flaws, but large annoyances. They must affect anyone that has this class of machine that is a clone, so wondering what people are doing for fixes/improvements.
I'll let it slide that the tipped screws that come with the lathe are so long they interfere with the cover when supporting anything .75 or over (you know, like a barrel). I drilled and swaged some copper into shorter ones, that when I realized that you can't remove the end gear cover to change gears without removing the spider screws all together... Ugh. Any reason I I shouldn't just take a hole saw and drill that sucker out to be the full diameter of screws?
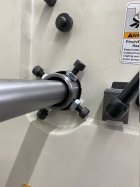
Second thing I didn't notice when looking at the lathe initially was that the cross slide is indexed 90 degrees of the other lathe I've been using. This means for threading I am at 60.5 degrees on the face, not 29.5. I can live with that. But I haven't quite figured out how I'm going to get to crowning angles reliably (and quickly) without the scale going to 90. I could come up with some form of witness marks at 10 degree but that doesn't help me much beyond a one or two specific angles. Am I having a brain fart here or is there an easier way?
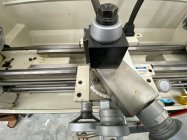
If anyone has other gotchyas I'm going to encounter on this machine, please feel free to chime in!
After a good cleaning and alignment it appears the bed has a slight spring in it that I still need to get sorted out for working down the bed, but through the headstock all indicates as well as I might have hoped.
I've come across two things that seems like obvious design flaws for a "gunsmithing" targetted lathe though. Well maybe not design flaws, but large annoyances. They must affect anyone that has this class of machine that is a clone, so wondering what people are doing for fixes/improvements.
I'll let it slide that the tipped screws that come with the lathe are so long they interfere with the cover when supporting anything .75 or over (you know, like a barrel). I drilled and swaged some copper into shorter ones, that when I realized that you can't remove the end gear cover to change gears without removing the spider screws all together... Ugh. Any reason I I shouldn't just take a hole saw and drill that sucker out to be the full diameter of screws?
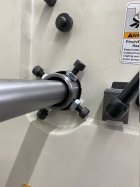
Second thing I didn't notice when looking at the lathe initially was that the cross slide is indexed 90 degrees of the other lathe I've been using. This means for threading I am at 60.5 degrees on the face, not 29.5. I can live with that. But I haven't quite figured out how I'm going to get to crowning angles reliably (and quickly) without the scale going to 90. I could come up with some form of witness marks at 10 degree but that doesn't help me much beyond a one or two specific angles. Am I having a brain fart here or is there an easier way?
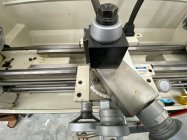
If anyone has other gotchyas I'm going to encounter on this machine, please feel free to chime in!
Last edited: