jackieschmidt
Gold $$ Contributor
Monday we will start setting up to align bore the shaft line for the big Cutter Head Shaft on this Dredge.
The shipyard will finish all of the welding in of the new bearing bosses this week end. The bearing bosses will be finished bored to 12.370 diameter. The last picture is of a fixture I made to align the wire with the large gearbox shaft.
The bearings will be water lubricated Duramx Cutless Bearings Pressed in.
www.duramaxmarine.com
I will take some pictures as we are setting up. I will be using our 14 foot long 4 inch bar.
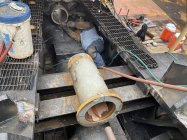

The shipyard will finish all of the welding in of the new bearing bosses this week end. The bearing bosses will be finished bored to 12.370 diameter. The last picture is of a fixture I made to align the wire with the large gearbox shaft.
The bearings will be water lubricated Duramx Cutless Bearings Pressed in.
Johnson Cutless (Cutlass) Water-Lubricated Rubber Bearings
Johnson Cutless, the original, true Cutlass bearing, only available from Duramax Marine. These rubber bearings have oil resistant nitrile polymer lining.
I will take some pictures as we are setting up. I will be using our 14 foot long 4 inch bar.

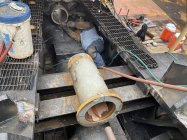
