jackieschmidt
Gold $$ Contributor
I am at Sterling Shipyard in Port Neches Texas this week align boring the Stern Tubes on a 5000 HP Harbor Tug.
They have been having problems, and finally determined that the Stern Tube Bearing and Inboard Shaft Seal are not where they are supposed to be.
Working off of a laser, we are align boringp the Stern Tube so they will be in alignment with the reduction gear and strut.
The vessel has eleven inch diameter shafts. We are boring approx 1/2 inch to the side out to make rom for a pressed in sleeve that the bearing will mount in. The finished bore with 3 steps is a nominal 13 3/4 inches diameter.
It’s about a four day job. We finished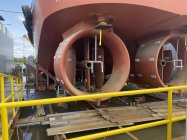
the Port Side yesterday evening and are now set up on the Starboard side.
Here are some pic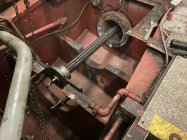
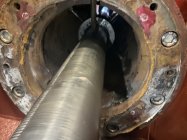
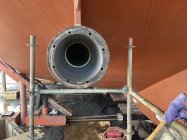
They have been having problems, and finally determined that the Stern Tube Bearing and Inboard Shaft Seal are not where they are supposed to be.
Working off of a laser, we are align boringp the Stern Tube so they will be in alignment with the reduction gear and strut.
The vessel has eleven inch diameter shafts. We are boring approx 1/2 inch to the side out to make rom for a pressed in sleeve that the bearing will mount in. The finished bore with 3 steps is a nominal 13 3/4 inches diameter.
It’s about a four day job. We finished
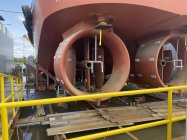
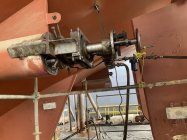
Here are some pic
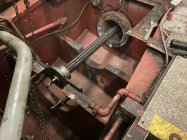
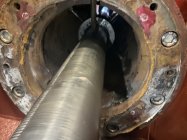
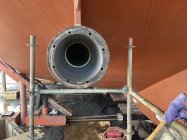
Last edited: