LVLAaron
Gold $$ Contributor
Ultimate Reloader got this idea from Bruce Thom (BAT Machine).
It's a machined-in-place tailstock holder made from an MT-Jacobs adapter. The merits are appealing. Very rigid, very simple, and if machined properly should be dead nuts to the specific machine.
I'm curious if one could machine it well enough to achieve the desired effect. Adjusting a single-point boring bar in a 4-6 jaw chuck seems difficult for the desired accuracy. If the hole is oversized even a few tenths, you'll end up with oversized chambers.
What say you, internet?
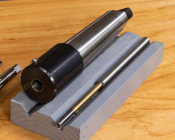
It's a machined-in-place tailstock holder made from an MT-Jacobs adapter. The merits are appealing. Very rigid, very simple, and if machined properly should be dead nuts to the specific machine.
I'm curious if one could machine it well enough to achieve the desired effect. Adjusting a single-point boring bar in a 4-6 jaw chuck seems difficult for the desired accuracy. If the hole is oversized even a few tenths, you'll end up with oversized chambers.
What say you, internet?
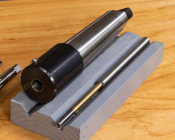