Firstly thanks to Gina for initiating this post and the healthy, lively and creative responses it has generated.
After finishing my GinaErick annealer I’m sharing my experience for the benefit of other to learn as I learnt from the many posts here.
In no particular order:
- Using a cheap eBay LC meter (LC100A) the original 1000W induction coil measured 1.5micro henry, the 8 turn 1.125 inner diameter 3mm replacement coil measured 1.1micro henry.
- With no load the induction board draws 9.5A (much higher than expected), with full load my PSU gives 11.1A and unfortunately that seems to be its maximum regulated current despite being advertised as 12.5A. The 9.5A might be due to the coil being lower inductance than the original, I will do further testing on the next one I build.
- Not all brass is created equal. ADI brass was annealed for 9.2secs and tempilaq melts 1mm below the shoulder, it has been through the annealer 20 times and still looks new (obviously that is test only piece). At 9.3s 11.1A the ADI brass was just starting to glow as a ring around the ring of the mouth where the brass has been chamfered thin. The Federal Premium brass at 9.2s was glowing red hot and is toasted. Obviously different calibres require different anneal times, but also be very careful that your set anneal time for a certain calibre is across brass of exactly the same type (don’t mix your brass!)
- The 11.1A maximum supply is contributing to the longer time to hit 750F on the neck, I’m concerned that the heat is soaking the body staying in the coil that long. 400F tempilaq on the body melts from the shoulder down about 1/5 of the case. To shorten the anneal time I’ve ordered a 1000W supply replacing the 600W unit, this should decrease the anneal time with higher current available and stop heat soaking down the case body. The temperature is probably OK but the risk of it not being OK and failing when firing encouraged me to resolve it properly.
- The 1000W unit has a nice feature that it shows set voltage and maximum current limit setting, the models recently on Banggood also include remote potentiometers to set those parameters. By being able to control the maximum current will, as other contributors have pointed out, gives greater control over different cases without having to rely purely on heat time given that the actually energy into the case can otherwise vary. To make use of the current limit setting will require me fitting some externally accessible electrical points to short out the 48V output as that is the process to set that parameter.
- Before winding the 3mm copper tube on the mandrel I slipped a heat shrink tube over it so that the final product would have insulation between turns. After wrapping, gently shrink the tubing so that air pockets can escape, prevent trapped air bulging, before using on the induction board. Rather than join the coil to the larger copper pipe I sleeved the copper pipe at the points where it connects to the board, ie solder an outer copper sleeve around the thinner coil. This allowed the coil pipe flowing the coolant to extend past the board and not risk leaks onto it….though maybe the longer piping is contributing to my higher no-load current draw through some eddy current effect.
- Admittedly I didn’t read every post before setting out on my build. I wish I had read the post recommending fitting the pump high to aid in removing air bubbles naturally. Anyway, rocking and rolling the unit eventually bled the air.
- Initially I used a 12V 70A truck relay to switch the 48V supply to the heater thinking the massively over-rated current allowance would allow for the higher voltage. The relay lasted 10 cycles before smoke came out. A 40A unit I had at hand lasted 1 cycle, possibly opening the relay and bending the contact arms as others described would have prevented them getting fried. The induction board is, not surprisingly, highly inductive so contact tips work hard. I have some 60V schotyky diodes on order and will trial those across the board as freewheeler to see if that reduces voltage spikes.
- The next replacement relay was a solid state SSR-100 DD (100A 3-32V DC control switching 5-60V) sitting on a bed of heat compound bolted to aluminium angle bar. After 100 no load cycles the home-made heat sink was uncomfortably hot though probably wouldn’t have ever failed as they are designed to get pretty warm. The slow postal delivery of the heat sink (first one went missing in the mail) prompted me to go out and buy and fit a standard 240V AC coil relay consistent with Gina’s design. The simple solution is working perfectly (SY4044 Jaycar model).
- The only changes I made to Gina’s design was to add some indicators and a trapdoor option. Indicators for 240V, 12V, 48V supplies…not really necessary because the timer powers up with 240V and the voltmeter shows 48V but the 12V system indicator is handy. The other change was to add a small impeller flow indicator from Amazon to the cooling system so that I can see that the coolant is flowing, I will fit a small Perspex window in the top to be able to check it periodically; they seem to be sensitive to orientation, mine only wants to spin in the horizontal position, be wary of trapping air bubbles in the impeller so orientate to allow them to pass. Maybe friction on the spline overcomes the gentle flow (3mm pipe is very restrictive) when not horizontal. The trapdoor has a pushbutton so that I can activate it, this is handy to immediately drop a case out, also handy to check it is working before adding the first piece of brass and test the 12V supply is on. With that option you don’t really need a 12V indicator as a working solenoid indicates 12v available.
-
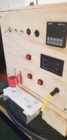
The build has been a great project to work on and very enjoyable so thanks again to Gina. I’m already planning the next mod or maybe new build using a DPS5020 panel that will precisely and easily control the current limit.