I have recently taken up crafting rifle stocks and have learned a lot in the last year or so. I have learned a lot on this forum and picking a few other people's brain. I craft a few for friends, some for sale, and some for myself. I would like to share my process of fabbercobbling, for those interested. So ladies and gentleman welcome to my empire of dirt.
I start out by searching the interwebs for quality pieces of lumber. Sometimes that is via eBay or craigslist for local saw mills. I have made a few connections with local clearing/logging contractors to find decent raw pieces but they still need drying and boarding out. Also just like with anything you can pay $50 for a piece of wood that is mediocre but maybe a great piece to learn on. Or you could buy a gorgeous piece for thousands of $$$. There are entire dissertations on figure/curly/birdseye etc on what constitutes a pieces "grade" but I dont want to get into that.
I try to find pieces that have some nice figure that are not crazy pricey and fit my measurement requirements. I generally search for a piece that is at least 30-36" in lenght, 6-8" in width, and depending on the design idea 2-3" in thickness. A larger piece is always better than a piece too small. The more beautiful pieces grab your attention at first but some aren't the measurements I am looking for.
Once I find a piece that seems to be worth it I run it through a planer. This gets the piece flatter and easier to make cuts with the bandsaw.
This piece shown below that I will be showing some of the process with was originally sold as a mantle piece. It was larger than I needed so I was able to get two stock blanks from it. 52" long x 10-3/4" wide x 2-3/4" thick. I had it shipped to my door for $137.79
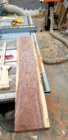
After the piece goes through the planer I select a "template" that I have made for the outline
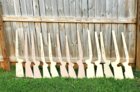
Once I select a template I layout the basic outline and try to place the template in areas that miss the sapwood or large knots. Luckily this piece didn't have any troublesome knots, just some sapwood on one side. Then the blank is cut from the slab and I can move on to the next steps.
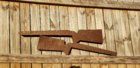
Depending on how well I cut the blank with the bandsaw, I will either run the top across the jointer or smooth out the top with a hand plane. ( Some of these photos are from different stock but its the same process)
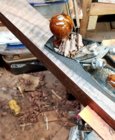
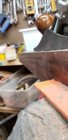
Then blank is cut and ready to be measured up for the initial inletting.
I start out by searching the interwebs for quality pieces of lumber. Sometimes that is via eBay or craigslist for local saw mills. I have made a few connections with local clearing/logging contractors to find decent raw pieces but they still need drying and boarding out. Also just like with anything you can pay $50 for a piece of wood that is mediocre but maybe a great piece to learn on. Or you could buy a gorgeous piece for thousands of $$$. There are entire dissertations on figure/curly/birdseye etc on what constitutes a pieces "grade" but I dont want to get into that.
I try to find pieces that have some nice figure that are not crazy pricey and fit my measurement requirements. I generally search for a piece that is at least 30-36" in lenght, 6-8" in width, and depending on the design idea 2-3" in thickness. A larger piece is always better than a piece too small. The more beautiful pieces grab your attention at first but some aren't the measurements I am looking for.
Once I find a piece that seems to be worth it I run it through a planer. This gets the piece flatter and easier to make cuts with the bandsaw.
This piece shown below that I will be showing some of the process with was originally sold as a mantle piece. It was larger than I needed so I was able to get two stock blanks from it. 52" long x 10-3/4" wide x 2-3/4" thick. I had it shipped to my door for $137.79
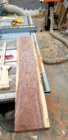
After the piece goes through the planer I select a "template" that I have made for the outline
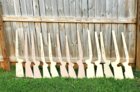
Once I select a template I layout the basic outline and try to place the template in areas that miss the sapwood or large knots. Luckily this piece didn't have any troublesome knots, just some sapwood on one side. Then the blank is cut from the slab and I can move on to the next steps.
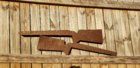
Depending on how well I cut the blank with the bandsaw, I will either run the top across the jointer or smooth out the top with a hand plane. ( Some of these photos are from different stock but its the same process)
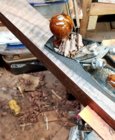
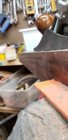
Then blank is cut and ready to be measured up for the initial inletting.
Last edited: