Where is a good source for expanding mandrels?
CW
Edit
Explanation, I have a Sinclair expander die and several of the basic expanders for turning necks. I would like to test with different mandrels to "tinker with" neck tension.
CW
Here's my response to a different post:
I know that everyone likes to control neck tension with bushings but to me that doesn't seem like a very good way. From my way of thinking bushings transfer any variance in neck thickness to the inside of the neck where they have a direct impact on neck tension. That is not a good thing, because no matter how careful you are turning necks there will be variances, and those variances will impact neck tension.
I believe that the outside of the neck has minimal importance. The only important thing is how thick the necks are because that has an influence on spring-back. IMO the part of the neck everyone should be focusing on is the inside of the neck, or more appropriately inside diameter. The inside diameter is what influences neck tension, if one can transfer neck wall variances to the outside of the case it is that much better.
So the question is how do we control neck tension from the inside of the neck? What if instead of honing die necks (an irreversible and often problematic process because dies are hardened, not to mention that you have to be twice as accurate with a die then with a mandrel, an impossible taskfor most small machine shops) we were to use a mandrel to expand the necks to provide the desired neck tension? What would a mandrel do?
Well, ... a mandrel would control the inside diameter of a case neck much more precisely than any bushing ever can. It could also transfer neck thickness variances to the outside of the neck where it doesn't interfere with neck tension and bullet release. That's good isn't it?
I have been using mandrels for thousands of cases. The problem is that just when I have a mandrel that gives ideal neck tension (down to .0001 precision) it starts to wear, and after a couple of thousand cases it is done. Making another mandrel to .0001 precision is very difficult/not possible for most machine shops and grinding shops. So I set out to look for a solution. I eventually focused on the Hornady bullet puller collet, because that's what I had. I started using the bullet puller to hold pin gages to expand the necks to match the turner mandrel.
However, the bullet puller did not hold the pin gages as co-axially straight as I wanted, so I approached Kenny Porter, who is master machinist for all kinds of things including parts for pacemakers (can you think of anything more critical?). I told him I wanted him to make a die for me that would hold a pin gage, actually a range of pin gages ie .305, .306, .307, .308 and .309. Once I showed him what I had in mind he made a leap to a collet that is ideally suited for what I wanted. The collet holds the cutting bit for a CNC machine. It has real holding power.
Pin gages are small tubes 2" long and can be bought for a few dollars and they are available in dimensions as exact as .0001 (+/- .00002). They generally have a 60 to 62 Rockwell hardness, like tool steel. They are ideal for this purpose, all you have to do is bevel the tip.
Well, ... to make a long story short Kenny Porter (kennethp@portersprecisionproducts.com) made this die for me . The collet he used is made for CNC machines so it holds mandrels perfectly straight with great strength. This mandrel die makes all other mandrel die I have seen or bought look primitive.
Regards
Joe
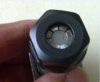