I'm doing this for school project. First I model a Remington 700 bolt and processed to start modifying to make sure it would be right. This is .308 bolt
1st I pulled the prints off PTG and Badger sites (PTG uses a 45 degree off set, Badger uses 30 degrees)
For the bushing I'm going to use .625 OD which is stated for magnum. But since there is no measurement called out for .308 or .223 I'm left to use this one. Or go with a slightly smaller bushing like .500 OD
If you look at the print: (download here: https://www.badgerordnance.com/wp-content/uploads/2013/10/306-90_91_92_Extractor.pdf)
Of the pocket view
The issue is the cut of .115 doesn't appear to be deep enough.
Here is to show my reference point (OD of the bolt) and depth is correct per the drawing. The bolt body is .696 OD and the bolt nose is (lugs forward to bolt nose) is 0.693OD. I'm measuring the bolt I have off my factory rifle.
It seems the correct way is to mill the slot deeper, but how deep? In the model I could use guess and check to find it would take .145 cut to get completely through bolt body to rid the area in pink squares above.
1st I pulled the prints off PTG and Badger sites (PTG uses a 45 degree off set, Badger uses 30 degrees)
For the bushing I'm going to use .625 OD which is stated for magnum. But since there is no measurement called out for .308 or .223 I'm left to use this one. Or go with a slightly smaller bushing like .500 OD
If you look at the print: (download here: https://www.badgerordnance.com/wp-content/uploads/2013/10/306-90_91_92_Extractor.pdf)
Of the pocket view

The issue is the cut of .115 doesn't appear to be deep enough.

Here is to show my reference point (OD of the bolt) and depth is correct per the drawing. The bolt body is .696 OD and the bolt nose is (lugs forward to bolt nose) is 0.693OD. I'm measuring the bolt I have off my factory rifle.
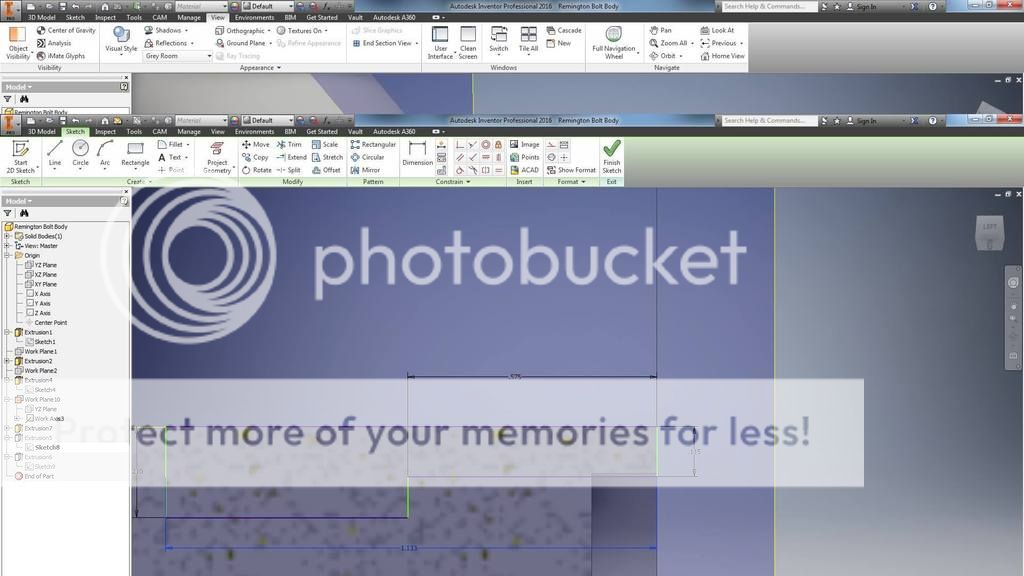
It seems the correct way is to mill the slot deeper, but how deep? In the model I could use guess and check to find it would take .145 cut to get completely through bolt body to rid the area in pink squares above.