RegionRat
Gold $$ Contributor
This was a good summary of the stuff that happened long ago, but folks like to reinvent the old problems when they try to skimp on maintenance or push things too far. Nothing new about it, still happens when new folks rotate through the food chain.I used to do metallurgical failure analysis. Could you explain what you thought made the brass poor quality. Did it contain junk like metal oxides. Most molten metals at some time in melting and processing are carried in cast iron vessels. They can pick up oxides from the pots and molds. The oxides are stress risers. I'm, lucky I never had a real neck splitting problem. I may have lost 5-10 cases in 50 years. It's been 11 years since I retired. I cross sectioned about 20 cases and gave them a metallographic polish and examined them on an optical microscope. They always contained very small black particles. Never did EDS on them. Without reviewing I think AMPS website shows black specks of particles in their etched metallographic pix.
Good machinery is one thing, but no matter where we are discussing it is up to the folks that run and maintain the machines and processes that make the difference.
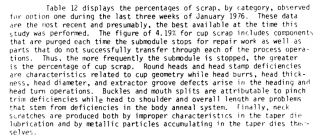
During the cupping operation, if the cups or alloys allow contamination, and the die lubricants and coolants are not very clean, then the problem just carries through the whole process. Starts and stops make things worse too, so general machine maintenance also opens the door for the scrap rate to climb, and escapes then follow.
I recently opened cases of factory ammo that contained split necks in both 223 and 204. I have also seen split necks in 17 HMR after firing (I collect that brass to keep it from going on the ground using an AR style brass catcher).