As I mentioned in another thread, I recently bought a Webster Hardness Tester (it's a counterfeit) to get a better idea of what my annealing efforts were actually like. Am reporting back with what I've observed after doing some testing to see how this tester might help.
It's always been my objective to try and anneal my brass to a hardness at or close to what new brass is. . . like Lapua's brass. But I never had any way to take any kind of measurement and would just anneal to what I thought would be close enough. It was really nothing more than guess work. Now that I have this Webster Harness Tester, I can get some idea where I'm at. Though I know it's not going to give me what I'd call "accurate" real harness number, I'm after a way to put consistent test numbers together in order to compare how what I do with annealing to how factory brass comes ready to load.
When I measured quite a few different lots of Lapua virgin brass the reading was just under 15 (like between 14.5 and 15). Measuring Peterson virgin brass, the hardness reading was just over 15. Therefore, I set my target measurement to be at 15, at which point my brass is ready for loading.
Grabbed some .308 once fired range brass (PPU's to be specific) and used them to test and get some idea for the timing in the annealing process. I'd vary the amount of time in the flame and after the cases would cool down, I'd take a measurement. Then I'd run another anneal session at a different time. . . and so on. Before I'd anneal my Lapua cases, I took some measurements on my fired cases that have been fired 14 times and annealed after every firing and got a consistent reading of 17. Previous annealing's were all done with the "glow method" having the case drop out of the flame the moment the necks began to glow in a darkened room. Then the sizing and the rest of the case prep was done.
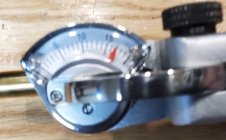
One of the things I found with the various testing I did with the PPU cases, what how much the sizing process changed the hardness. I really had to leave the case in the flame a lot longer to get the hardness indication well below my target so that with my sized cases, the hardness was then at my target indication. I had to get my fired Lapua brass down to a 13.
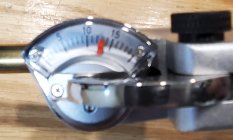
After FL sizing and expanding the necks to my target diameter the hardness rose to my target indicated hardness of 15.
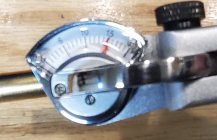
Keep in mind, I wasn't just measuring just one piece of brass, but several pieces as I wanted to see the consistencies, if any. The tool showed me very consistent results. Again, I don't know exactly what the hardness is. But I do know that my final hardness measurement is now the same, or very close to the same, as my various lots of .308 virgin brass.
Somewhat of a surprise to me was how much additional time I had to leave the cases in the flame to get that 13 reading that I needed. In the past, when I use the "glow method" it was about 5 seconds in my swirl flame torch and that would get the reading just under a 15. But then the sizing process is what would move it up to 17 and why all my previously anneal brass measures 17. Now, to get that reading of 13 before sizing, I have to leave the cases in the flame for 10 seconds
. . . and the neck glows pretty good for a few seconds, obviously (as seen in a darkened room).
Once I get my box of Lapua brass processed, I'll have to see if I need to make any adjustments to "neck tension" and how they feel when seating projectiles, and. . . what the chrono and targets report.
I've got a box of 2x fired formed Lapua brass that I annealed just a few years ago. The timing of that annealing was done by watching for a yellow flame (no glowing) and dropping the cases out of the flame then. The result of the hardness test was an 18 (after sizing of course).
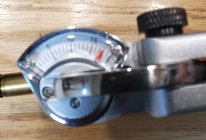
Sorry about the picture quality. Had a hard time holding the tool properly and getting a pic taken at the same time.
It's always been my objective to try and anneal my brass to a hardness at or close to what new brass is. . . like Lapua's brass. But I never had any way to take any kind of measurement and would just anneal to what I thought would be close enough. It was really nothing more than guess work. Now that I have this Webster Harness Tester, I can get some idea where I'm at. Though I know it's not going to give me what I'd call "accurate" real harness number, I'm after a way to put consistent test numbers together in order to compare how what I do with annealing to how factory brass comes ready to load.
When I measured quite a few different lots of Lapua virgin brass the reading was just under 15 (like between 14.5 and 15). Measuring Peterson virgin brass, the hardness reading was just over 15. Therefore, I set my target measurement to be at 15, at which point my brass is ready for loading.
Grabbed some .308 once fired range brass (PPU's to be specific) and used them to test and get some idea for the timing in the annealing process. I'd vary the amount of time in the flame and after the cases would cool down, I'd take a measurement. Then I'd run another anneal session at a different time. . . and so on. Before I'd anneal my Lapua cases, I took some measurements on my fired cases that have been fired 14 times and annealed after every firing and got a consistent reading of 17. Previous annealing's were all done with the "glow method" having the case drop out of the flame the moment the necks began to glow in a darkened room. Then the sizing and the rest of the case prep was done.
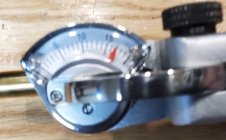
One of the things I found with the various testing I did with the PPU cases, what how much the sizing process changed the hardness. I really had to leave the case in the flame a lot longer to get the hardness indication well below my target so that with my sized cases, the hardness was then at my target indication. I had to get my fired Lapua brass down to a 13.
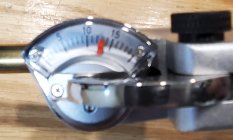
After FL sizing and expanding the necks to my target diameter the hardness rose to my target indicated hardness of 15.
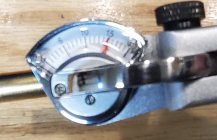
Keep in mind, I wasn't just measuring just one piece of brass, but several pieces as I wanted to see the consistencies, if any. The tool showed me very consistent results. Again, I don't know exactly what the hardness is. But I do know that my final hardness measurement is now the same, or very close to the same, as my various lots of .308 virgin brass.
Somewhat of a surprise to me was how much additional time I had to leave the cases in the flame to get that 13 reading that I needed. In the past, when I use the "glow method" it was about 5 seconds in my swirl flame torch and that would get the reading just under a 15. But then the sizing process is what would move it up to 17 and why all my previously anneal brass measures 17. Now, to get that reading of 13 before sizing, I have to leave the cases in the flame for 10 seconds

Once I get my box of Lapua brass processed, I'll have to see if I need to make any adjustments to "neck tension" and how they feel when seating projectiles, and. . . what the chrono and targets report.

I've got a box of 2x fired formed Lapua brass that I annealed just a few years ago. The timing of that annealing was done by watching for a yellow flame (no glowing) and dropping the cases out of the flame then. The result of the hardness test was an 18 (after sizing of course).
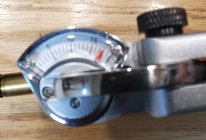
Sorry about the picture quality. Had a hard time holding the tool properly and getting a pic taken at the same time.

Last edited: