jackieschmidt
Gold $$ Contributor
I mention on occasion that we do precision straightening of large Prop Shafts and Rudder Stocks rhat come out of Push Boats.
I had to do this yesterday, one of our customers dropped it off.
For those that do not know, a Rudder Stock is a vertical shaft in a boat that the rudder blade is welded on to. The upper portion fits in a tube with a bearing at the bottom and one at the top of the rudder tube. There is a tiller arm installed on a keyed taper at the very top all held together by a large not.
this is our smallest “straightening rig”. It has. 175 ton Jack. We have three more, a 300 ton, a 500 ton, and a 750 ton.
Straightening things like this with massive tonnage is as much of an art as it is a skill. You have to analyze exactly where the bend begins, and work it out. The arms are adjustable, so you can place tonnage at any specific point and make the piece straighten exactly where you want it too. We have a graduated 10,000 PSI gage on out pumps so I know exactly how much tonnage I am applying.
I call this “applying precision tonnage”.
We do quite a bit of this. Some as large in diameter as 12 inches.
here is a couple of pictures of before, with the rig in place, and after straightening.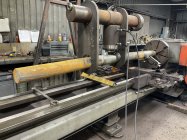
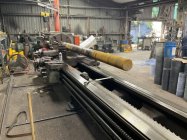
one thing to note, this puts no strain on the lathe. All of the pressure is contained in the straightening rig.
I had to do this yesterday, one of our customers dropped it off.
For those that do not know, a Rudder Stock is a vertical shaft in a boat that the rudder blade is welded on to. The upper portion fits in a tube with a bearing at the bottom and one at the top of the rudder tube. There is a tiller arm installed on a keyed taper at the very top all held together by a large not.
this is our smallest “straightening rig”. It has. 175 ton Jack. We have three more, a 300 ton, a 500 ton, and a 750 ton.
Straightening things like this with massive tonnage is as much of an art as it is a skill. You have to analyze exactly where the bend begins, and work it out. The arms are adjustable, so you can place tonnage at any specific point and make the piece straighten exactly where you want it too. We have a graduated 10,000 PSI gage on out pumps so I know exactly how much tonnage I am applying.
I call this “applying precision tonnage”.
We do quite a bit of this. Some as large in diameter as 12 inches.
here is a couple of pictures of before, with the rig in place, and after straightening.
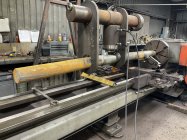
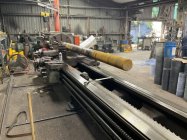
one thing to note, this puts no strain on the lathe. All of the pressure is contained in the straightening rig.
Last edited: