scasa
Silver $$ Contributor
I'm getting ready to start on a new project and needed to upgrade my milling head for my lathe . I've made one of these before but that was about 30 years ago and although it worked really well it had it's faults. Number one was square tubing isn't square or flat , I fixed that on this one by milling the 2 and 1/2 inch tubing flat first thing . I didn't have a mill when I made the first one. The other drawback was the arbor that holds the cutting tool, I had to make them and in different sizes for different diameter tools. they weren't the best or most accurate plus you had to change the whole arbor to go to different diameter tools . Although it worked ok I wanted an upgrade. Now I have internet and amazon prime so I got an ER 16 collet shaft and a set of collets 1/32 to 3/8. the collet shaft was 20 mm in diameter and I found a couple of new 20mm bearings still in the box in my used bearing can and I got two pieces of 2 1/2 inch square tubing from the fab place for just the cutting charge. So about 4 days later this is what I ended up with.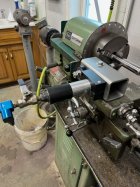
It's powered by an air motor similar to a die grinder but with a planetary gear reduction . it runs about 2000 RPM . Power gets to the collet shaft via two 40 tooth pulleys and a 10 mm wide cog belt giving it a 1 to 1 ratio. Now you wont be hogging off a 1/4 inch cut with a 1/2 inch end mill but it cuts extractor slots really well and since it was made and bored on my lathe its on the centerline with the spindle. It doesn't have any up and down adjustment but I can raise it up with riser blocks. Look behind the chuck on the lathe and there is an indexing disk the holes are every 5 degrees plus a few extras and a locking pin to lock it to the hole and a clamp bolt to hold it solid. I also have a 90 to 1 right angle gearbox that mounts to the spindle on the end so I can mill and rotate at the same time. Poor mans rotary table. I have 3 different disks, one has the hole pattern for cutting the locking lug slots for a centerfire receiver with a full diameter bolt where the lugs are at the front. This how I cut the locking lug recess for the lug opposite the bolt handle on my .22 receivers.
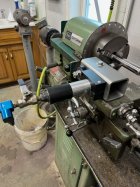
It's powered by an air motor similar to a die grinder but with a planetary gear reduction . it runs about 2000 RPM . Power gets to the collet shaft via two 40 tooth pulleys and a 10 mm wide cog belt giving it a 1 to 1 ratio. Now you wont be hogging off a 1/4 inch cut with a 1/2 inch end mill but it cuts extractor slots really well and since it was made and bored on my lathe its on the centerline with the spindle. It doesn't have any up and down adjustment but I can raise it up with riser blocks. Look behind the chuck on the lathe and there is an indexing disk the holes are every 5 degrees plus a few extras and a locking pin to lock it to the hole and a clamp bolt to hold it solid. I also have a 90 to 1 right angle gearbox that mounts to the spindle on the end so I can mill and rotate at the same time. Poor mans rotary table. I have 3 different disks, one has the hole pattern for cutting the locking lug slots for a centerfire receiver with a full diameter bolt where the lugs are at the front. This how I cut the locking lug recess for the lug opposite the bolt handle on my .22 receivers.