I did some measurements yesterday and I need some info before I try anything.
The first question Is for people who index your barrels. Do you think I can use thickness between the bore and the outside of the muzzle to determine muzzle runout? Is that a fair indicator of where the bore is pointing? My thought is the thinnest measurement would indicate the bore is curved in that direction.
The second question is for anyone who makes barrels for savage rifles. What is the exact function of the inside bevel that I highlighted in the picture below? Is it necessary? if it is how small can you make it and still have proper function?
Thanks guys.
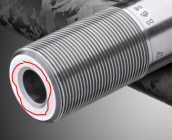
The first question Is for people who index your barrels. Do you think I can use thickness between the bore and the outside of the muzzle to determine muzzle runout? Is that a fair indicator of where the bore is pointing? My thought is the thinnest measurement would indicate the bore is curved in that direction.
The second question is for anyone who makes barrels for savage rifles. What is the exact function of the inside bevel that I highlighted in the picture below? Is it necessary? if it is how small can you make it and still have proper function?
Thanks guys.
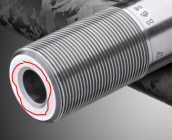